THE FORTRESS PROCESS
We have perfected a meticulous process that ensures every floor we coat receives the exceptional quality and durability it deserves. Our valued customers in Pennsylvania will have their floors coated and ready to use within one day from when our team arrives.
Here’s a glimpse into how we transform your floors with the best coatings for garage floors— premium polyurea coating.
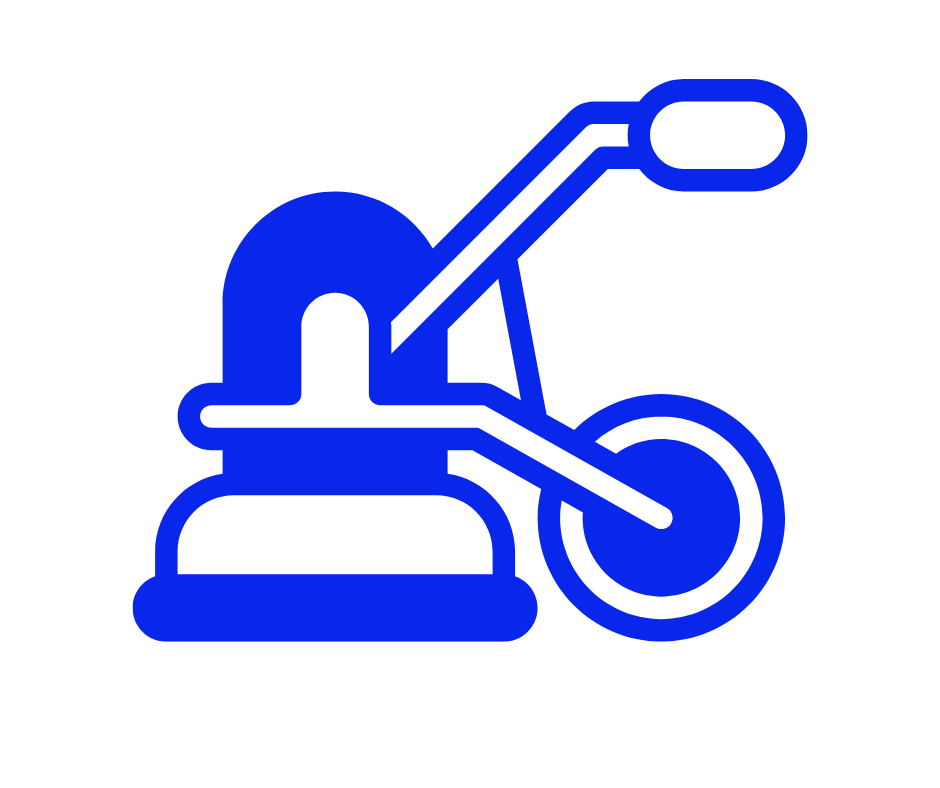
1.
Prepare, repair, and vacuum the concrete surface to ensure maximum adhesion.
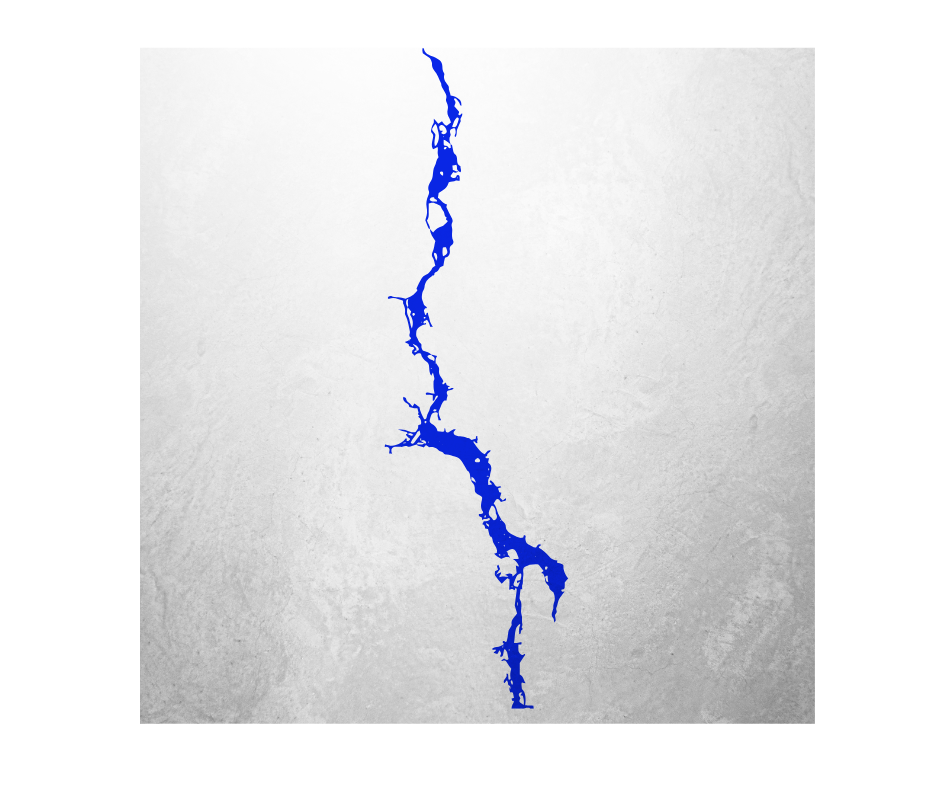
2.
We use 100% solids to repair cracks, ensuring a flawless surface before coating.
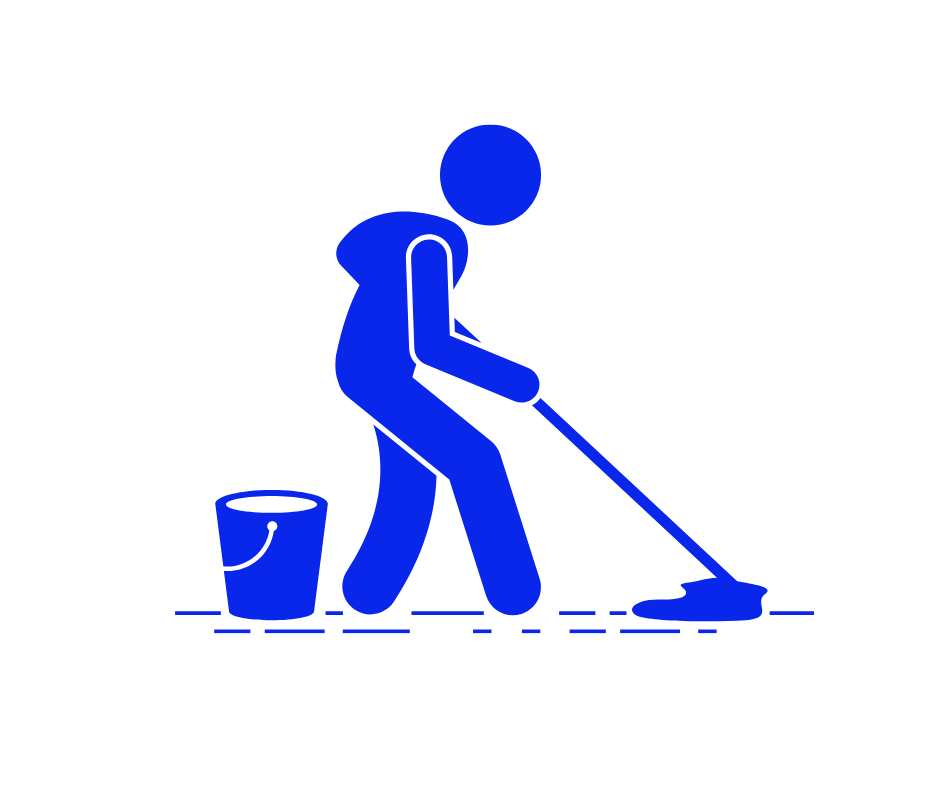
3.
We apply a self-priming pure polyurea base coat for unmatched durability and performance.
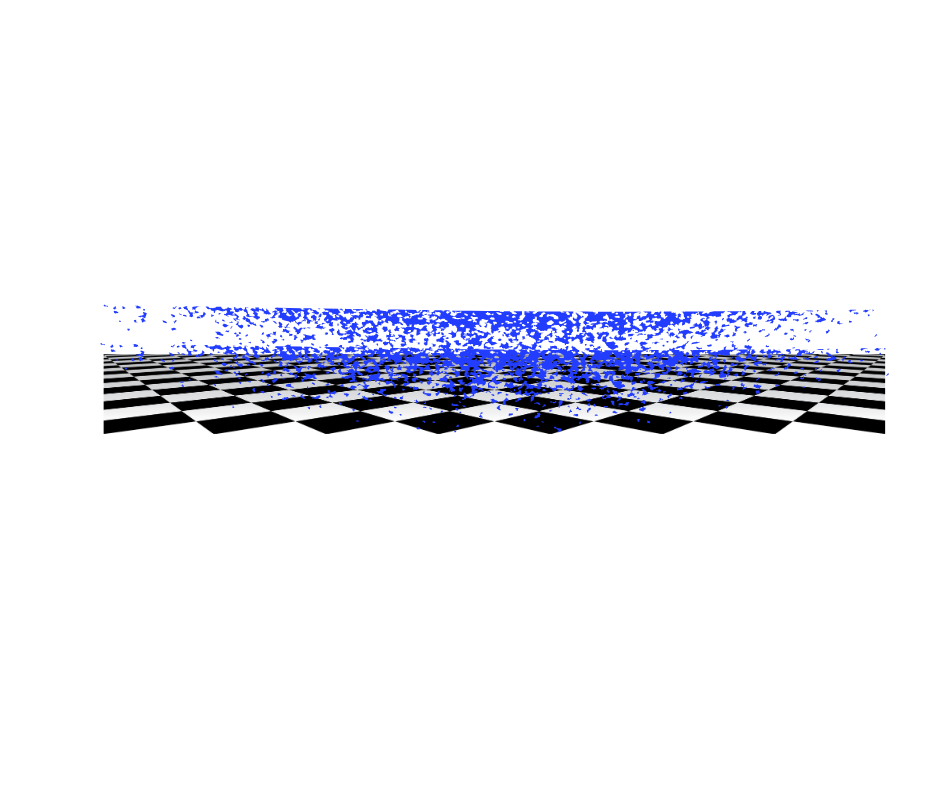
4.
We hand-broadcast polymer flakes generously, ensuring an even color and texture across the floor.
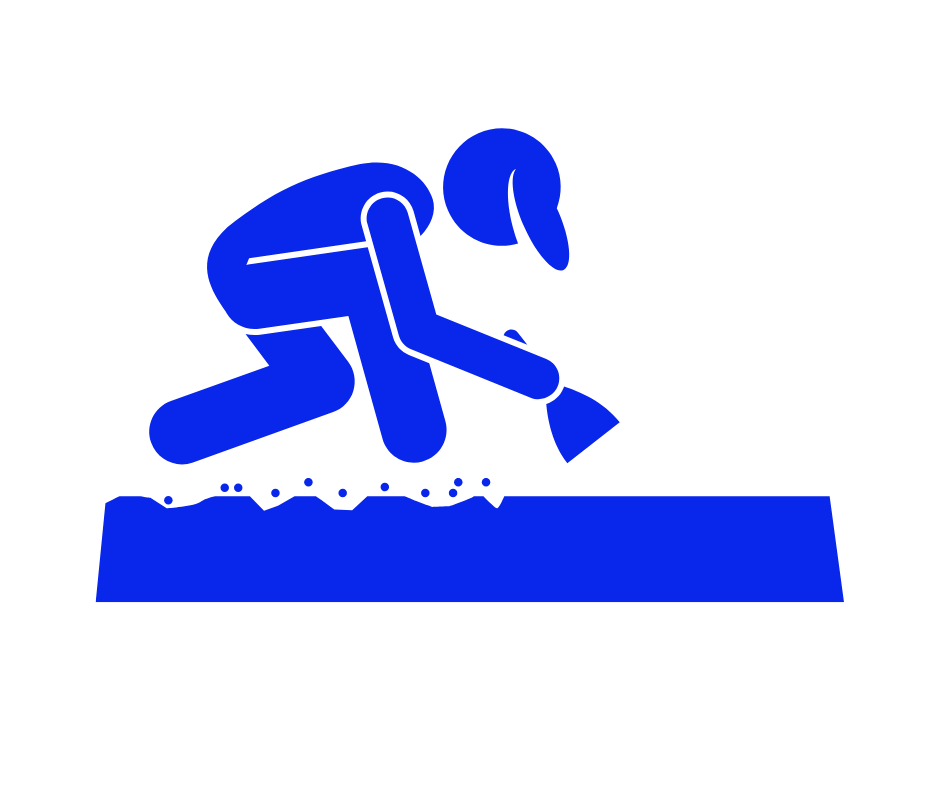
5.
We scrape off any excess flakes, leveling the floor perfectly in preparation for the final seal.
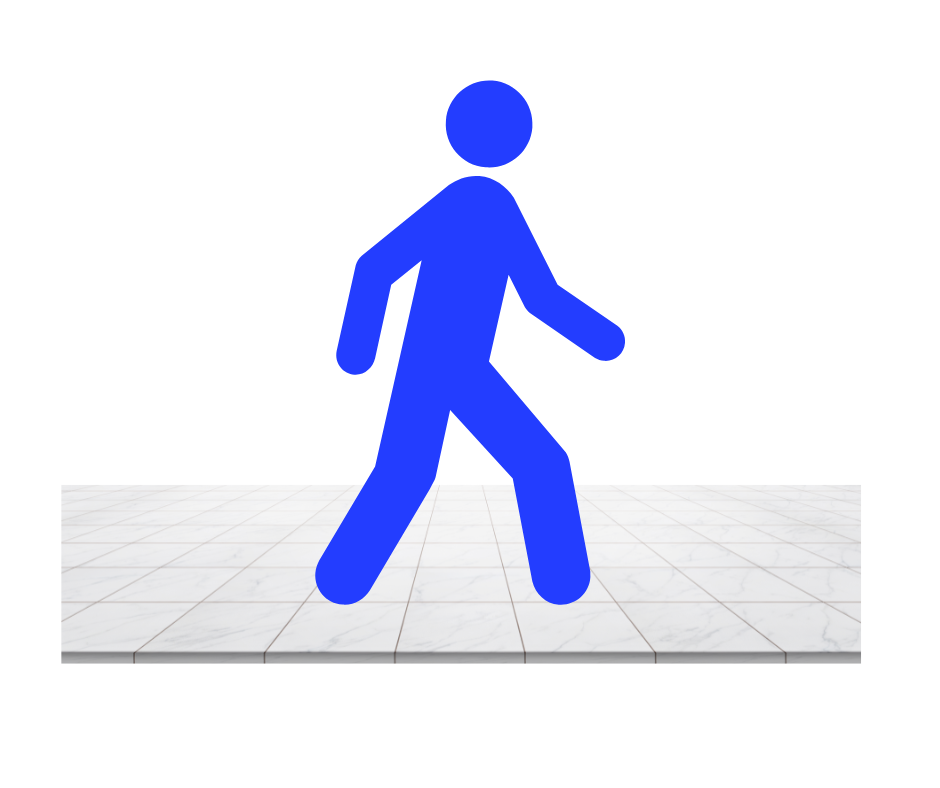
6.
Finally, we apply a UV stable topcoat. Your floor will be ready for traffic in 24 hours.
Why Fortress Floors’ Preparation Process Sets the Standard for Concrete Coatings
At Fortress Floors Pennsylvania, we understand that the key to a long-lasting, flawless concrete coating is in the preparation. That’s why we go above and beyond to ensure your garage floor, basement, or other concrete surfaces are meticulously prepped. Our detailed process guarantees the coating adheres perfectly, creating a durable, professional finish that stands the test of time. The Fortress preparation phase is key to achieving a strong bond between the coating and your concrete. Here is part of that process:
Grinding the Surface:
Using a diamond-bit Lavina grinder, we create a coarse, porous surface while removing any weak or deteriorated concrete. The grinder’s three wheels work together to open the concrete’s pores, and we use hand grinders for detailed areas and vertical surfaces.
Containing Dust:
To keep your space clean, we pair our grinders with high-powered vacuums that capture dust during the grinding process.
Removing Contaminants:
Spilled substances like oil, grease, or gas can penetrate concrete. Grinding usually removes surface-level contaminants, but for deeper stains, we apply a degreaser. Additionally, our specially formulated oil-based coating ensures proper adhesion, even if some oil residues remain.
Eliminating the Latent Layer:
The latent layer is the weakest part of the concrete and has minimal porosity. It forms during the slab’s original curing and must be removed for proper coating adherence. This layer is approximately 1/16th of an inch thick, so we grind to this depth to expose the stronger concrete beneath.
With meticulous preparation, we ensure your concrete floor is ready for its new coating—providing durability, beauty, and peace of mind.
Book Your Appointment
Get in touch via phone or by filling out the website form. This will help us discover what part of your house or business you want to coat and why.
Consultative Assessment
Our process begins with a thorough consultation. You can expect an in-depth assessment of your space to evaluate its condition, surface type, and any specific requirements. You’ll also receive a quote on the spot.
Floor Prep & Coating Application
If repairs are required before the polyurea application, our team will take care of them. We fix all pits and cracks to create a smooth surface. After the polyurea coating is applied, we conduct a rigorous inspection to guarantee the finish meets our stringent quality standards.
Post Installation Support
We provide guidance on how to care for your newly coated floors, ensuring they remain in pristine condition for years to come. In addition, every coating comes with a 15-year warranty.